Online Fulfilment Centre Stock Accuracy Variance Reporting
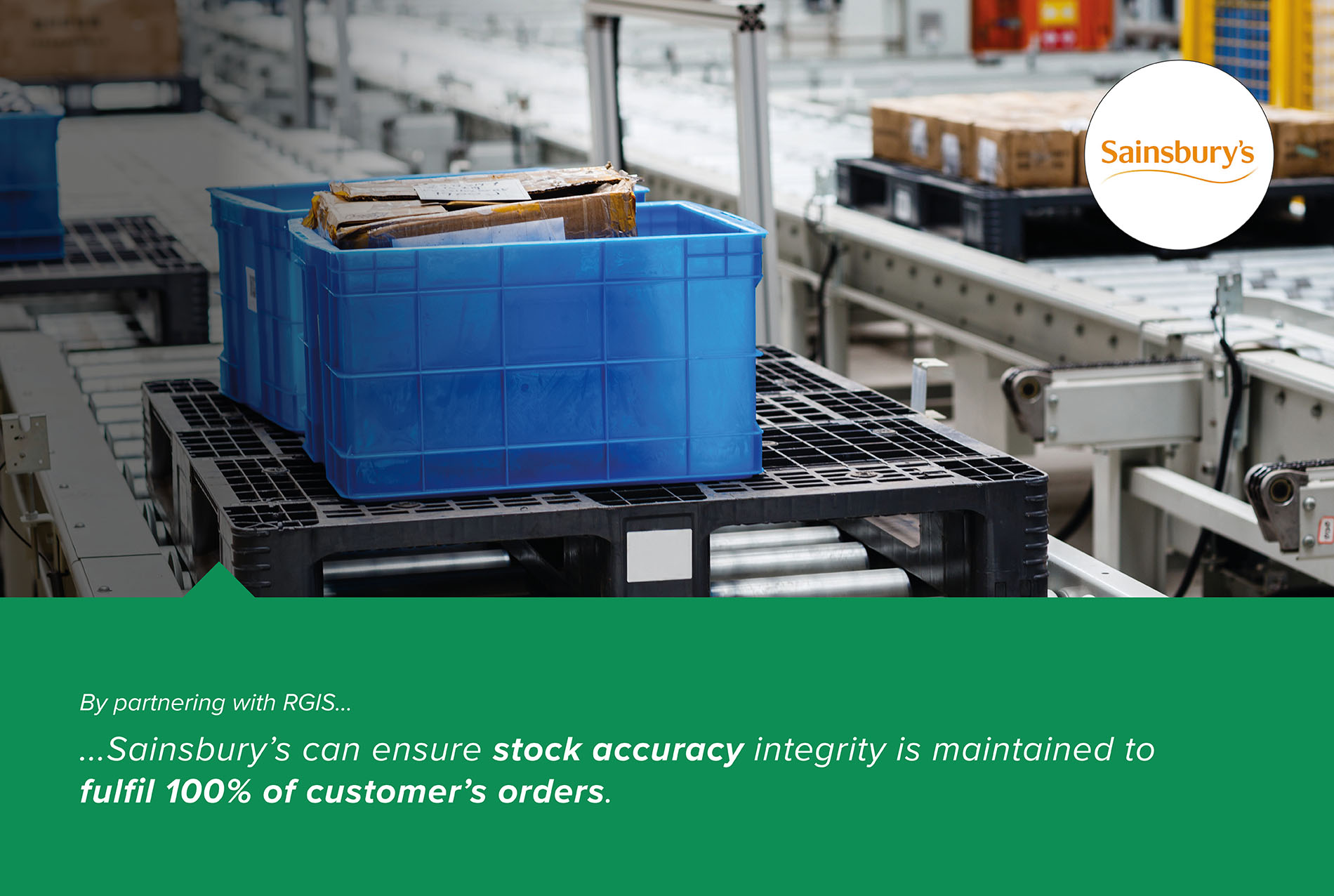
Sainsbury's, the UK's second largest grocery retailer with over 1,300 stores uses RGIS to count 90% of the store estate on an annual basis. This new requirement was to closely replicate the store count process in Sainsbury's online fulfilment centre in London, which serves customer online orders across London and the South East from a warehouse location.
REQUIREMENT
Sainsbury’s new requirement was to closely replicate the store count process in the online fulfilment centre in London, which serves customer online orders across London and the South East from a warehouse location. The customer required:
- RGIS to reset stock levels four times per annum across the site
- Ensure online orders are 100% picked and delivered
- To maintain 100% stock accuracy – stock accuracy is imperative in an online environment, to ensure no failed orders
SOLUTION
RGIS worked with Sainsbury’s and completed the following:
- RGIS sent 15 experienced auditors for a full day shift to the site, around the needs of the 24/7 pick and despatch operation
- The RGIS team counted approximately 25% of the volumes per visit, four times per year
- RGIS counted approximately 500 bin locations each visit
- Compared counted quantities, to the expected on-hand quantities per location, across grocery and general merchandise items
- Any variances found were then keyed back into the live stock system to maintain 100% stock accuracy
RESULTS
By partnering with RGIS, Sainsbury’s benefited from the following:
- Sainsbury’s corrected approximately 5% of lines
- Ensured stock accuracy integrity was maintained to fulfil 100% of customer’s orders
- Due to high turnover of orders, the operation from RGIS needed to be covert and non-intrusive to the day-to-day running of the site. RGIS’ close relationship with the site, ensured this was achieved successfully