Improving Inventory Management for Aviation Parts with Advanced Vision OCR Technology
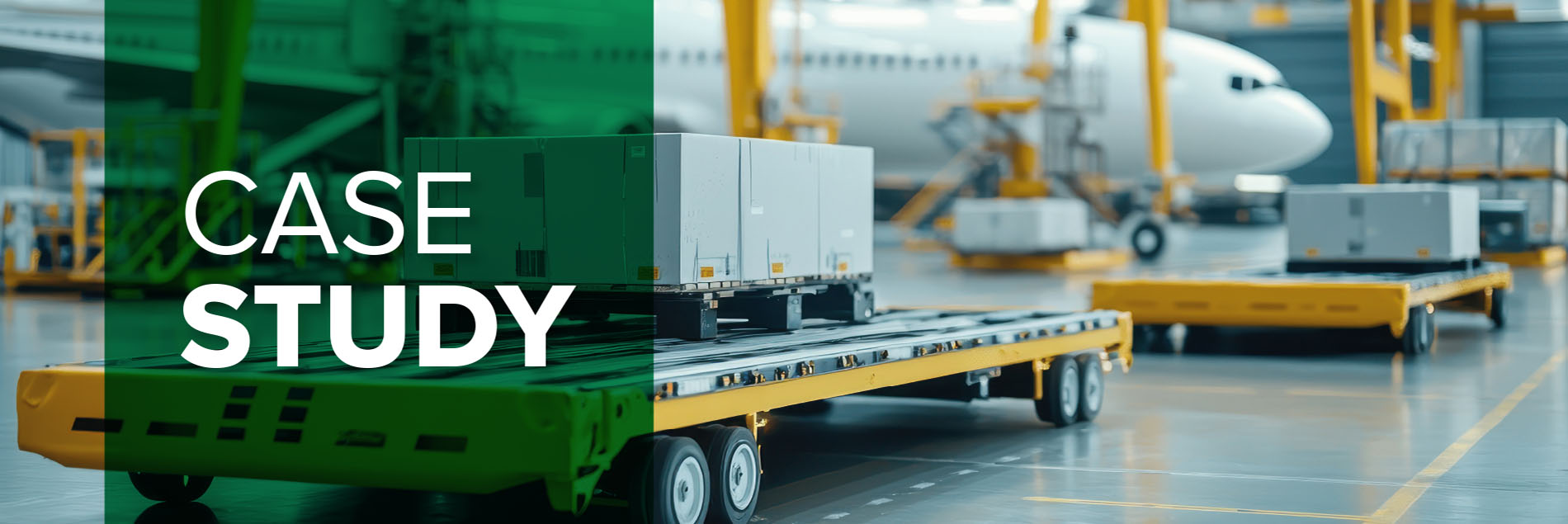
As the airline company is required by law to perform a complete inventory of these goods every two years, the company needed a reliable and innovative solution to manage the inventory efficiently while maintaining data accuracy.
CHALLENGE
An airline company that operates multiple warehouses for aviation parts and consumables, managed by both national and private sector companies, required the support of RGIS. These warehouses do not share a unified warehouse management system (WMS), resulting in incomplete and inconsistent data for inventory control. Additionally, some parts labels lacked critical information, making the inventory process challenging.
WHY RGIS?
After several years of considering other providers, the airline company selected RGIS for its innovative Vision OCR technology, which provided a competitive edge in automating data collection. This technology was crucial for overcoming the challenge of incomplete information on part labels and enabling more efficient inventory counts.
OUR SOLUTION
RGIS employed a systematic approach to handle the complexities of this inventory project:
- Daily Inventory Segmentation: To avoid disrupting daily warehouse operations, the inventory was divided into manageable daily segments. RGIS teams scanned parts and consumables across the bin locations, using Vision OCR to capture alphanumerical codes from the labels and update the system accordingly.
- Real-Time Data Processing: A Supervisor oversaw the real-time processing of the data collected by the scanning teams. Three key files were uploaded daily: the main data file (used by the NGEN Vision module), the daily database, and a range data file to track completed bin locations and identify any missing information.
- Daily Reporting: Each day’s inventory results were sent to the airline company representatives within 5 hours of the count’s completion. This allowed the customer to review the data and address any discrepancies, ensuring accuracy in their system. Variance reports highlighted an 18% discrepancy between stock and physical count, primarily due to misplaced items.
RESULTS
- Accurate Inventory with OCR Technology: The use of Vision OCR and daily variance checks ensured an accuracy rate of 98.9% after adjustments. RGIS identified over 2,000 products that were not listed in the system and should not have been there. Additionally, more than 900 outdated parts were found, prompting the airline company to reconsider the status of these items.
- Time Efficiency: RGIS completed the inventory in 46% less time compared to the company’s previous provider, significantly improving the project’s efficiency.
- Customer Satisfaction: The airline company was highly impressed with RGIS’s ability to provide daily reports, enabling them to manage the open warehouse environment more effectively. The customer also appreciated RGIS’s handling of complex challenges, such
as the need for handwritten code entries.
CONCLUSION
The airline company has expressed strong interest in continuing their partnership with RGIS, particularly for a partial inventory audit in the coming year. The success of this project, combined with the advanced Vision OCR technology, has positioned RGIS as a preferred partner for future inventory management services.